In our first post, we explored what catalysts are and how they have been instrumental in human development. In our second post, we look at one application specifically, producing energy. For over 100 years catalysts have transformed how we get from A to B, and as will see, will continue to do so by giving us cleaner greener alternative fuels.
By Aditya Sengar, Research Associate in the Department of Bioengineering.
“The Chinese use two brush strokes to write the word crisis. One brush stroke stands for danger; the other for opportunity. In a crisis, be aware of the danger but recognize the opportunity.” The quote by John F. Kennedy, the 35th President of the United States, has stood the times and is quite relevant in context to the catalysis industry today. Set in motion by the two world wars, the industry paved the way for the world to transition from a coal-based economy to crude oil-based economy initially. Now the industry is trying to transition us out of the oil-based economy.
End of the coal era
The world witnessed the dangers of excessive reliance on coal at the end of the 19th century because of rising air pollution by coal burning. London recorded the highest air particulate concentration in the 1890s. The discovery of crude oil in the 1850s was considered the status quo of the future of energy during those times. Crude oil consists of long carbon-chain molecules that need to be broken down to smaller chain molecules like the petroleum products we are more familiar with: petrol, diesel and aviation fuels. Thermal cracking, an industry standard until the 1940s, required burning crude oil at high temperatures to produce the petroleum products. The process was still dirty. Catalytic cracking, developed and refined in the 1930s in the USA, produced higher-octane fuels which served an edge to the Allied forces fighter aircrafts over their German counterparts. The process soon replaced thermal cracking in crude oil refineries. Modern day catalytic cracking involves catalyst in powder form with molecular cage-like structures at nanoscales that hold longer-chain crude oil and provide ion-exchange reactions for an easy breakdown to petroleum products.
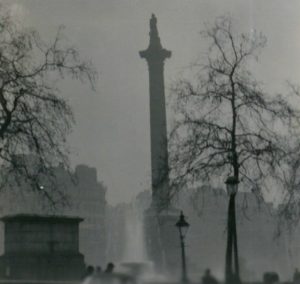
1970s energy crisis
In the 1970s, another energy crisis hit the western world. With oil supply saturating in Germany, USA and Venezuela, crude oil price rises rose and led to a decade long economic. The crisis also gave wind to the public’s views on the environmental effects of using coal and crude oil on the planet. The catalyst industry stood up to the task and developed processes for cleaner production of energy using coal, natural gas and oil or sometimes even replacing them.
Clean energy from coal
After the first world war, Germany was producing 14% of its energy supply by synthetic liquid fuel. Liquid fuel has its advantages over coal for being much easier to transport. This is the time before crude oil became the go-to energy resource. The process developed by German chemists Fischer and Tropsch was slowly faded into obscurity because of discovery of vast crude oil reserves across the world making oil a cheap commodity. The 1970s energy crisis made global powers, that were heavily reliant on coal, realize the commercial opportunity provided by the Fischer-Tropsch (FT) process. South Africa now produces 30% of its transport fuel using FT synthesis. The process works with molecular catalysts, called zeolites, with cage-like molecular structures to trap gases like, carbon monoxide and hydrogen[1], and make them react in a series of reactions to produce petroleum products. Modern-day research focuses heavily on reducing carbon dioxide, generated as a by-product of the process, via another catalytic method known as carbon capture and storage.
Biofuels and the struggle to replace crude oil
Biofuels are the alternative to crude oil derived diesel fuels and are produced by a catalytic process where vegetable oils from certain crops, like rapeseed and soybean, react with simple alcohols to form longer carbon chain molecules, the biodiesel. This is not a well-known fact, but the inception of a sustainable energy economy was actually kicked-off by biofuels. It was Nicolaus Otto, the father of the modern internal combustion engine, who first demonstrated an engine running on peanut oil as early as in 1900. Again, huge discoveries of crude oil reserves in the next few decades killed the interest in biofuels. Thanks to the 1970s energy crisis, the industry has since re-emerged and looks stronger than ever now. Although the calorific value (energy in kWh produced per kg of substance) of biodiesel is still 10-20% less than traditional diesel, the cost of production per unit of energy generated is similar. Production of biodiesel still has secondary effects like greenhouse gas emissions by excessive farming and increase in cost of the crops used as feedstock for the biodiesel production. The Paris Agreement of 2016 makes it binding for the signatories to produce 10-15% of their energy requirements by biofuels in the coming decade which is not a very ambitious mission provided the stage the technology is in right now.
Efficient production of electricity from natural gas
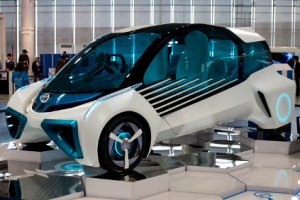
Two-thirds of the world’s electricity demand is fulfilled by fossil fuels of which majority is produced inefficiently by coal and natural gas. Furthermore, present-day gridlines to supply electricity to our homes and industries result in heavy energy loss. This results in overall low efficiency (about 33%) of converting primary energy source to usable energy. Enter fuel cells. A fuel cell generates current from a chemical reaction between hydrogen and oxygen over platinum catalyst with 60% efficiency. The oxygen comes from the air. Hydrogen production still requires natural gas (via a process called steam reforming). The produced hydrogen is suitably compressed, stored in a tank, and is replenished at a filling station, like petrol. Over the past 15 years, fuel cell cost has been brought down by 5 times to about $50/kWh (current costs of conventional internal combustion engines are about $30/kW for light-duty vehicles). A major cost of developing a fuel cell goes in the platinum catalyst used as electrode in the cell. Hyundai and Toyota, major automobile companies, are spearheading this initiative to have 31 hydrogen fuel cell powered car models on the road by 2025.
In the final part of this blog series, we will see exciting challenges faced by the catalyst industry and get a glimpse at a possible fossil-free carbon neutral world.
[1] The reactants are more commonly known as syngas, a product of coal gasification. Gasification is a process of reacting coal with a controlled amount of oxygen at high temperatures.