A simple guide to solar fuels 3 – Finding the best material for the job
Last time we asked how we could improve materials such as Fe2O3 (haematite), and how novel materials with more suitable properties could be found. In this, our final post, we will see how computers can help find the perfect material for the production of solar fuels. Finally, we will introduce the key steps that are usually done in a research lab to build a tangible device, a device that can be used to produce a “solar fuel”.
By Dr Miriam Regue and Dr Minsu Park, Research Associates in the Department of Chemical Engineering.
Predicting the properties of potential light absorber materials is an excellent starting point to evaluate their suitability as candidates for solar fuels devices. For example, the Computational Materials Science group focuses on modelling and simulating materials for solar energy conversion applications. Computational modelling allows us to predict the absorption properties as well as understand the inherent features of existing or new material candidates before building a tangible device. For instance, oxide perovskites are a class of light absorbing materials that are gaining significant interest in the field of solar fuels. Some examples are lanthanum ferrite (LaFeO3), praseodymium ferrite (PrFeO3) or gadolinium ferrite (GdFeO3); they are made of large abundant element and offer good visible light absorption but their understanding for solar fuels production is still scarce.
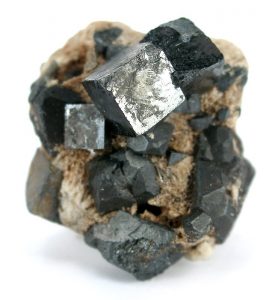
Computers are an excellent tool to predict material properties. They are so powerful that we can use them to run calculations and predict some of these unknown material properties. The results of these calculations help scientists to design a more efficient experimental approach to improve the solar fuel performance. They can acquire knowledge on how thick the material needs to be for boosting light absorption, how chemical modifications can affect the performance and how different structures of the same material can alter the optoelectronic properties.
Once the theoretical knowledge is gathered, the race on designing an efficient device begins. From a practical point of view, the successful material candidate must be stable in water conditions for at least 2,000 hours and provide a solar to fuel efficiency of at least 10%.
But how can we make a device that can be used to produce a ‘solar fuel’?
The first stage of the experimental design is to test the light absorber material at a lab scale. This is usually done following two different experimental approaches: (1) By depositing the light absorber material on top of a flat conductive surface to form a photoelectrode. This photoelectrode generates electric current upon solar light irradiation (photoelectrochemistry) and the electric current is used to produce the solar fuel. (2) Or alternatively, by directly immersing a powdered material in a reactor (photocatalysis) that is illuminated with solar light. Using this approach we can also measure and quantify the amount of solar fuel (i.e H2 (and O2), CO, CH4 …) produced (see the below diagram). Although both approaches are feasible for solar fuels production, thephotoelectrochemical approach is often the preferred one mainly for safety reasons, but also due to better reproducibility in results.
As simple as it seems though, there are numerous challenges that experimentalists face, such as low efficiencies and performances, and poor product selectivity and scaling-up reproducibility. Different experimental approaches are currently under investigation to address some of these issues. In our research group, we follow various novel approaches to improve the response of these materials and to understand and describe their behaviour. For instance, we recently discovered that (1) mimicking the shape of natural desert roses on TiO2, (2) using a polymer as a template for the preparation of LaFeO3 and Fe2O3, and (3) loading copper and graphene oxide on novel halide perovskite materials improves the performance and efficiency of the water splitting process and solar CO2 conversion to methane and carbon monoxide upon solar light irradiation (below diagram).
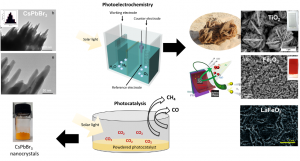
So, which technology readiness does solar fuel production have right now? Will we ever power our home using a stand-alone H2 device? Is our society ready to produce commodity chemicals (plastic, fertilizers, clothes…) from waste CO2 using solar light?
Unfortunately, photoelectrochemical approaches are still in lab-scale studies, but tremendous improvement has been achieved since their discovery in 1972 by Fujishima and Honda.2 Researchers have achieved solar-conversion efficiencies of 10 % for ca. 40 h and it is expected that similar or even higher efficiencies will be obtained by 2025 on square metre devices with the final goal to achieve a decentralised and local production of solar fuel (H2) at a household level in the near future. Direct CO2 capture and solar conversion is on a similar technological readiness as H2 production. However, the success of this technology relies on the capability of coupling direct CO2 capture technologies with photoelectrochemical set-ups. But undoubtedly, what will mark the deployment of these disruptive technologies and ensure a proper share in the current market is the ability to compete economically with conventional methods of hydrogen and carbon-based products production. Currently, steam methane reforming produces H2 at an average cost of ~ 1.40 $/ kg (it depends on natural gas price), is significantly lower than what is currently estimated for photoelectrochemical devices ( 9 – 11 $ kg-1).[1] However, if the research community manages to overcome the current technical barriers, the cost of hydrogen via photoelectrochemical methods could reach 2 – 4 $ kg-1.[2] This will be an extraordinary breakthrough that will pave the way for solar hydrogen to be included in the future energy mix.
Bibliography
- R. J. Detz, J. N. H. Reek and B. C. C. Van Der Zwaan, Energy Environ. Sci., 2018, 11, 1653–1669.
- B. A. Pinaud, J. D. Benck, L. C. Seitz, A. J. Forman, Z. Chen, T. G. Deutsch, B. D. James, K. N. Baum, G. N. Baum, S. Ardo, H. Wang, E. Miller and T. F. Jaramillo, Energy Environ. Sci., 2013, 6, 1983–2002.