I’ve mentioned the rig building project already, but let’s refresh the basics again:
“Construction of a closed system rig to independently control level and flow rate of water between two tanks. Water must be delivered from one tank to the other tank while maintaining levels. No by pass or recirculation in only one tank will be allowed.”
We had a week to come up with a design, and then 7 hours to build it. It sounds manageable, but we had a couple other deadlines, so it was terribly exhausting and most of the time I was happy to be able to stand straight and not fall asleep…
First of all, the design. As I mentioned, my father and I drew a very creative and cool design, but the team decided that it’s not practicable because of the lot of calibrations and several types of flexible tube requirements… So we ended up with a very-very-very simple design: one tube up, one tube down with 1 valve. I just called it the “boring” design, but since we had to do a presentation about the “features” of the rig before the demonstration, the “boring” was changed to “simple, cheap and easy to use”… Power of the language 🙂
The benefit of a simple design is that you don’t need a fancy P&ID (piping and instrumentation diagram), you don’t have a long inventory and the description is 2 paragraphs. So, after we submitted our design on Tuesday, we could almost forget about the whole thing till the next Monday… Of course, just almost… The funniest thing about the rig building project was how the entire class worked together: as we did it in two cycles, the first already finished it by the time we, the second, started. So, we could ask them about everything and exchange ideas… Therefore, we ended up collecting bits and pieces like “one valve is not enough” or “be there early to get the best aluminium struts” or “do the calibration excel beforehand” or “use gate valve instead of ball valve”. It was hilarious when the weekend before the construction, I got a message from my teammates in almost every hour, starting with “one of my friends from Cycle 1 said…”.
So, when we went there on Monday, we already changed our design quite a lot, based on “friend-informations”. We ended up having two outlets with two valves and a float switch in the upper tank. So, time to build it! The first 3 hours were mainly about the aluminium strut: who would have thought that screwing together 10 pieces of aluminium with 18 angle brackets using 3 allen keys is so difficult? Our team was allocated a space at the end of the lab – the furthest away from the workshop where all the pipes, screws or angle brackets were. So my job was to run back and forth between the workshop and our rig, finding the right lengths of copper pipes with the perfectly fitting nuts…
On the afternoon session we finished the piping and we were the first to pour water into our system! It felt so good, we were so “ahead”. And then, the float switch happened… When we tried to test it, it didn’t work! Firstly, we changed how the circuit was connected together. Then changed the float switch. Four times. Then asked a GTA. And 2 other GTAs as well. So after 1.5 hours of trial and error, we finally made it work, but we couldn’t start the calibration, because the session ended.
So we had to do all the calibration on Wednesday, in the remaining 1 hour. One hour!!!! We were there super early so that we could start at 09:00:00 🙂 In the first 15 minutes we quickly did the flow rate calibration, then in the remaining 45 minutes we did the flow level. It was terrible! After adjusting the valves, we had to look at the flow level and from the very little changes determine if it is constant or going somewhere. I thought we will run out of time when we only had 3 measurements done from the 15 and 20 minutes left, but somehow, magically, we finished all the calibration, did the documentation by 10:05 and even laminated it 🙂
The last half an hour was terrible but then the demonstration went very-very well: we had to do 10 and 20 L/min and 20, 50 and 70% flow level. The funny thing is that we only calibrated it for even levels (20,40,60 and 80), so the 50/70 were quite an improvisation 😀 But apparently the professors liked it because they gave us 20 As and 8 Bs which is awesome! So overall I was quite happy and despite the difficulties, I think this rig building was one of the best experiences in Imperial so far. And I made a picture before we took apart our system (in about 15 mins…), so here it is:
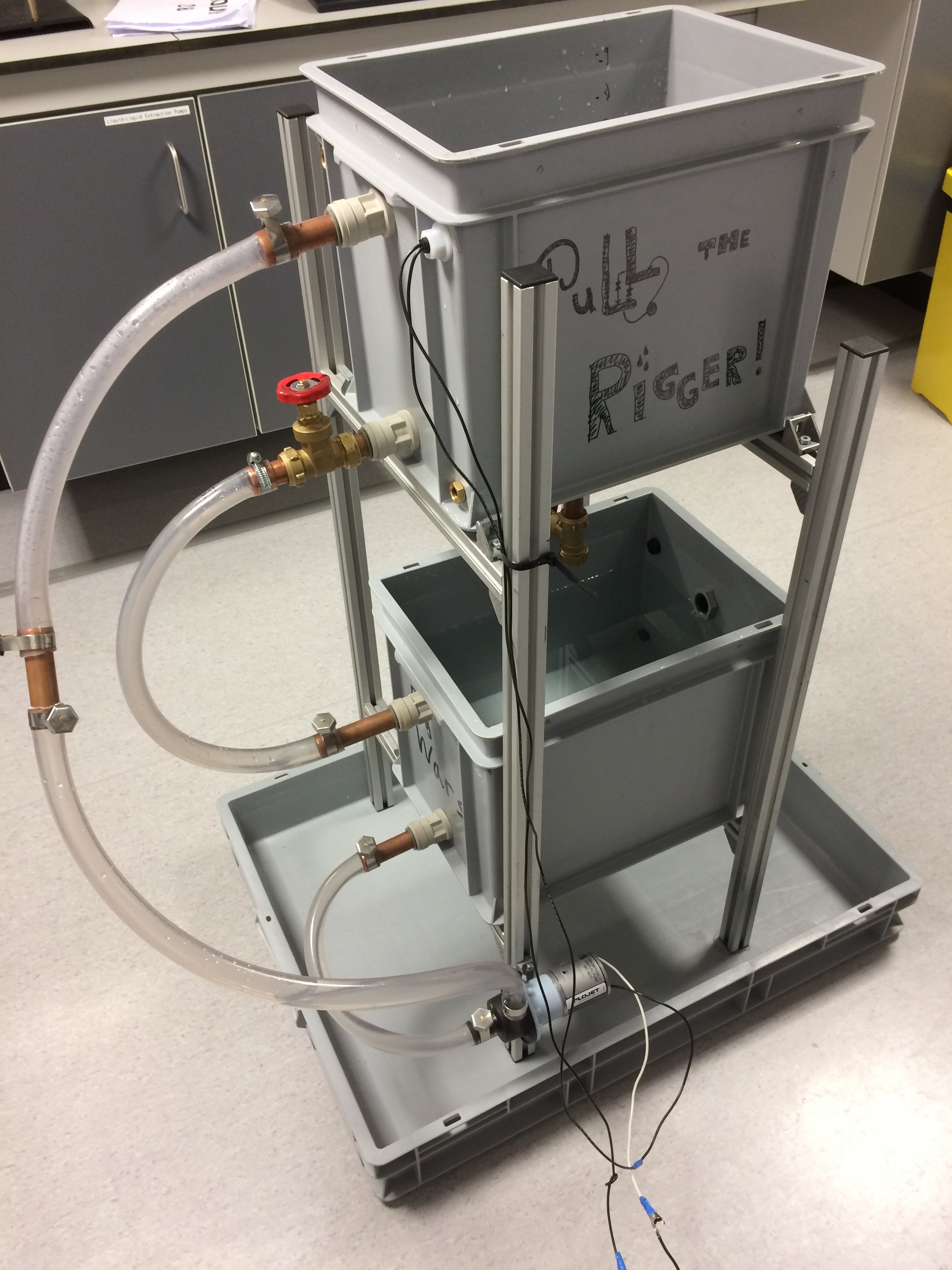
I recently heard that despite my initial belief that only my parents read my blog, there are actual real people out there who are interested in my stories… Thank you guys, I hope you like it! 🙂 And if you have any comments/questions, just post it down here and I’ll try and answer them 🙂